XSHELL
PAPER SHELL MADE OF CELL UNIT
ELECTIVE COURSE, FALL '19, CORNELL UNIVERSITY
IN COLLABORATION WITH YU SUN, MENGYI YAN, AND JUNSIK OH
XSHELL
PAPER SHELL MADE OF CELL UNIT
ELECTIVE COURSE, FALL '19, CORNELL UNIVERSITY
IN COLLABORATION WITH YU SUN, MENGYI YAN, AND JUNSIK OH
This project explores the simplest way of constructing a doubly-curved shell structure - by setting the fabrication method based on planar manufacture, which can be achieved by CNC Routers or laser machines and using sheet materials like chipboard. The cellular unit was mapped and unrolled to planar folding and cutting lines, fabricated through tens of recycling chipboards within 2mm thickness. The whole fabricating process including cutting, folding, and assembling took only 5 days and 3 group members to complete the construction of this human-scale installation on the 3rd floor of Sibley Hall.
This project explores the simplest way of constructing a doubly-curved shell structure - by setting the fabrication method based on planar manufacture, which can be achieved by CNC Routers or laser machines and using sheet materials like chipboard. The cellular unit was mapped and unrolled to planar folding and cutting lines, fabricated through tens of recycling chipboards within 2mm thickness. The whole fabricating process including cutting, folding, and assembling took only 5 days and 3 group members to complete the construction of this human-scale installation on the 3rd floor of Sibley Hall.
VOXEL LATTICE
A ROBOTIC PRINTED CAFE PAVILION
INTERNSHIP PROJECT, FALL '18, FAB-UNION TECHNOLOGY
SITE: WEST BUND VENUE B, SHANGHAI, CHINA
PROJECT SUPERVISOR: LIMING ZHANG AND PHILIP F. YUAN
Located at West Bund Venue B for the service of WAIC 2018, this cafe pavilion demonstrates the latest technology of robotic nodal printing. We concluded the printing path as a prototype of a linear element in design form. Hence, I started the design from the network rather than solid or volume. By defining an optimization rule of the three-way network, a planar grid under the influence of human flows was generated. After the grid was transformed to 3d network based on graphic statics and structural optimization, it was translated to a morphed printing tool-path, which also took some research and optimization. The pavilion demonstrates an autonomous process of design with the integration of knowledge about structural performance and craftsmanship.

Planar geometry starts with the ground relationship with the basement, which results in a three-way grid system. After disturbing the grid with simulated possible people routes, a series of rationalized disturbed grid curves come out to become the boundary and the basic planar curves.
After getting those basic curves, a particle system is introduced to simulate the real force situation of how they will bend taken into consideration of pure axial stress. Then the pulled curves are further subdivided and adjusted by parameters to make the whole structure become rationally stressed.

With our study of the planar generation rules, we applied them to the site. By studying the potential flows of people coming to the ground, the influenced grid patterns gradually centralized to the double-nested pentagon. We then made the inner part of it as our pavilion boundary and the outer part as the boundary of the pavilion. With the overall boundary of the pavilion defined, we then generated the body of the pavilion. The plan generation rule still acts as we define people flows as input disturbance curve and then get rationalized planar grid curves. Then we pull up boundary curves and grid curves respectively by Kangaroo engine. Finally, we further subdivide the grid and extract controlling curves to be prepared for further optimization. After the structural shape is generated, we optimize the stress of the designed surface through topological optimization plug-in Millipede. By adjusting the distribution of density of grid and the curvature of controlling curves, we got a series of results. We sort them according to their stress performance and chose one of the best results to be the final design.



The pavilion is divided into 6 sections and 47 pieces to print respectively. Each piece was printed in the factory and then assembled on site.
The generated grid is subdivided into both inner and outer parts. The two sides of the subdivided grid can form twisted boxes of one-to-one correspondence. Within one section, different pieces are linked through plastic strapped nodes. They are connected with the printed network.
With a targeted pavilion of such a big scale, it is divided into printable pieces of components. The division curves are based on a subdivided network and their positions control the size of each component.
After the boundaries of each component are defined, they are filled up with printing paths to be printed by robotic arms.
The structural performance of the printed network under different discretization strategies within a single voxel is simulated and physically tested to get the best performance for the target curving geometry.
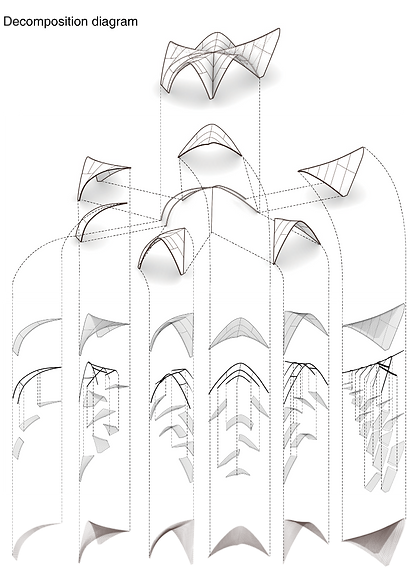
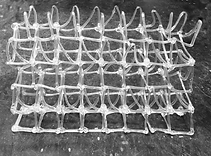



The pavilion takes a discrete construction strategy. The continuous geometry of the pavilion is pix-elated into a series of discrete components, each of which contains a unique crystallized printing tool-path. And as the stress on the overall form would be distributed into the pixels of the grid system, the entire network has to be modified into 5 types of different densities according to different structural performance along the surface. In the end, based on the support of digital design and robotic construction technology, the pavilion demonstrates the integration of structural performance analysis technology with the designed form and establishes a new model of production in the building industry.
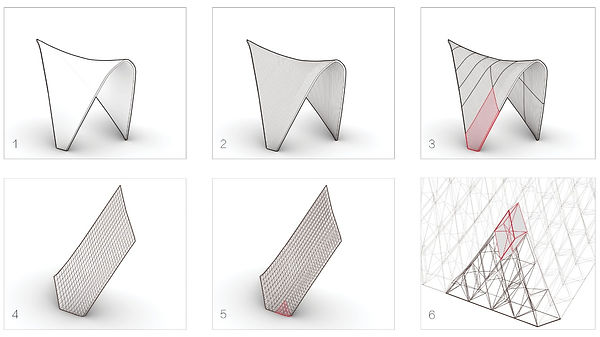

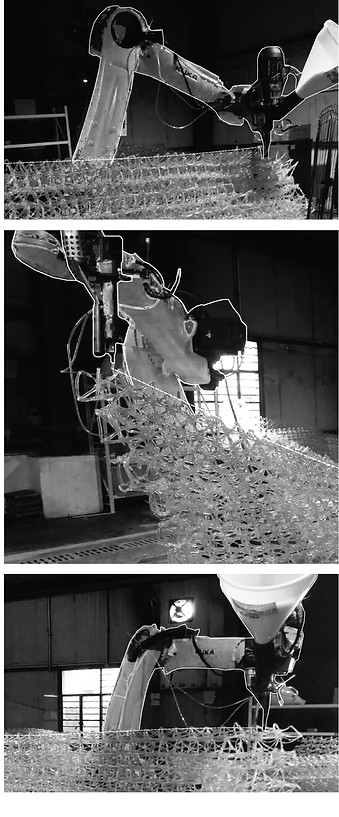

Move to new starting point, turn on extruder, be ready to print this cell.

Print bottom frames, wait one second at central point to form a node, then turn off extruder.

Rotate work plane to escape collapse with printed cells, move to new starting point to be ready to print next cell.

Move to new starting point, turn on extruder, be ready to print this cell.
