XSHELL
PAPER SHELL MADE OF CELL UNIT
ELECTIVE COURSE, FALL '19, CORNELL UNIVERSITY
IN COLLABORATION WITH YU SUN, MENGYI YAN, AND JUNSIK OH
XSHELL
PAPER SHELL MADE OF CELL UNIT
ELECTIVE COURSE, FALL '19, CORNELL UNIVERSITY
IN COLLABORATION WITH YU SUN, MENGYI YAN, AND JUNSIK OH
This project explores the simplest way of constructing a doubly-curved shell structure - by setting the fabrication method based on planar manufacture, which can be achieved by CNC Routers or laser machines and using sheet materials like chipboard. The cellular unit was mapped and unrolled to planar folding and cutting lines, fabricated through tens of recycling chipboards within 2mm thickness. The whole fabricating process including cutting, folding, and assembling took only 5 days and 3 group members to complete the construction of this human-scale installation on the 3rd floor of Sibley Hall.
This project explores the simplest way of constructing a doubly-curved shell structure - by setting the fabrication method based on planar manufacture, which can be achieved by CNC Routers or laser machines and using sheet materials like chipboard. The cellular unit was mapped and unrolled to planar folding and cutting lines, fabricated through tens of recycling chipboards within 2mm thickness. The whole fabricating process including cutting, folding, and assembling took only 5 days and 3 group members to complete the construction of this human-scale installation on the 3rd floor of Sibley Hall.
OPERATION PPE
FLAT-TO-CURVE FACE MASK
RESEARCH PROJECT, SPRING '20, SABIN LAB
TEAM MEMBERS: JENNY SABIN, MADDY EGGERS, BEGUM BIROL, YAO LU, ZHENXIANG HUANG, TENG TENG, VERONICA VARGA, COLBY JOHNSON, MAHSHID MOGADASI, ALEX HTET AUNG KYAW
The 3d-printed mask design acts as a fabric fitter to turn any material — fabric, felt, paper towel — into a viable face mask. the cuts in the design create a flexible “living hinge” that allows the 3d-printed material to take on double curvature for a secure, comfortable, and custom fit to the face. the mask is broken into parts that snap together in order to fit a standard 3d printer. anyone with a printer can rapidly produce these custom-fitted masks in under two hours, allowing an informal network of makers to augment gaps in the supply line in times of crisis.
This fabric fitter was designed as part of operation PPE by the Sabin Lab at Cornell University in collaboration with the Black Box at Princeton, an informal fabrication operation that leverages the participatory and networked space of design and making across disciplines to innovate design solutions to rapidly respond to gaps in supply chains at times of extreme crisis. the sabin lab launched operation PPE with collaborators at Cornell University on March 24th to respond to an urgent request from Weill Cornell medicine for PPE face shields. the initiative has since inspired clusters of makers and designers across the country and internationally. our new york-regional network of Cornell faculty, students, staff, alumni, and home 3d printing enthusiasts has since delivered over 25,000 face shields to regional and NYC-based hospitals. the sabin lab at Cornell AAP is a trans-disciplinary design research lab with a specialization in computational design, data visualization, and digital fabrication. our latest mask designs incorporate off-the-shelf materials and custom tools and algorithms such as the ‘living ‘hinge’ to address fit, comfort, and ease of fabrication through DIY 3d printing networks.
This design won third place in the Let’s Face It international mask design competition.

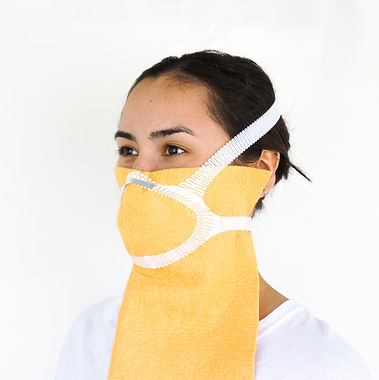
