XSHELL
PAPER SHELL MADE OF CELL UNIT
ELECTIVE COURSE, FALL '19, CORNELL UNIVERSITY
IN COLLABORATION WITH YU SUN, MENGYI YAN, AND JUNSIK OH
XSHELL
PAPER SHELL MADE OF CELL UNIT
ELECTIVE COURSE, FALL '19, CORNELL UNIVERSITY
IN COLLABORATION WITH YU SUN, MENGYI YAN, AND JUNSIK OH
This project explores the simplest way of constructing a doubly-curved shell structure - by setting the fabrication method based on planar manufacture, which can be achieved by CNC Routers or laser machines and using sheet materials like chipboard. The cellular unit was mapped and unrolled to planar folding and cutting lines, fabricated through tens of recycling chipboards within 2mm thickness. The whole fabricating process including cutting, folding, and assembling took only 5 days and 3 group members to complete the construction of this human-scale installation on the 3rd floor of Sibley Hall.
This project explores the simplest way of constructing a doubly-curved shell structure - by setting the fabrication method based on planar manufacture, which can be achieved by CNC Routers or laser machines and using sheet materials like chipboard. The cellular unit was mapped and unrolled to planar folding and cutting lines, fabricated through tens of recycling chipboards within 2mm thickness. The whole fabricating process including cutting, folding, and assembling took only 5 days and 3 group members to complete the construction of this human-scale installation on the 3rd floor of Sibley Hall.
RED PAVILION
DEPLOYABLE FORMWORKS W/ NEXORADE SUPPORT
INTERNSHIP PROJECT, SPRING '19 (COMPLETED IN FALL 19'), FAB-UNION TECHNOLOGY
SITE: WORLD INTERNET CONFERENCE, WUZHEN, CHINA
PROJECT SUPERVISOR: LIMING ZHANG, XIANG WANG AND PHILIP F. YUAN

The design workflow of 'Red Pavilion' at the Wuzhen World Internet Conference was based on a research studio in Spring 2019 with a target to utilize the large deformation of bending-active structures to enhance structural stability. For this research, a design framework was made from the initial form-finding of compression-only funicular shell structures to the bending simulation based on the dynamic relaxation method in Grasshopper, as well as the explicit analysis in FEM software.

Design strategy and the specific techniques in the research of bending active 3D-printed formwork for unreinforced thin shells (Left: Form-finding and optimization; Right: Simulation and analysis of the bending process).
The form-found doubly-curved geometry was further optimized to develop a surface that could be unrolled as a planar pattern for 3D printing. The global geometry was then stabilized with the V-shape cross-section from the corrugation of the bent plates and hence gained safety as well as redundancy.

Construction Process with the bent 3D-printed formwork.
After the printing of the lattice-formed elements of the formwork, a thick layer of polyurethane was cast on top and milled with the robotic arm according to the designed doubly-curved surface of the shell. The pattern design of the 3D-printed blocks was based on the original UV quadrilateral mesh of the form-found shell, and reformulated to a reciprocal structure with a so-called ‘nexorade’ pattern. This is mostly due to the low Young’s modulus of the ABS plastic so that the reciprocal structure can provide better stiffness than the quad-mesh.
Meanwhile, as the reciprocal pattern would bring the eccentricity of the adjacent edges that made the interior surface rugged, the ‘nexorade’ could decrease the extent of such eccentricity and also align the direction of new edges better along the original force vectors (Mesnil et al., 2018).
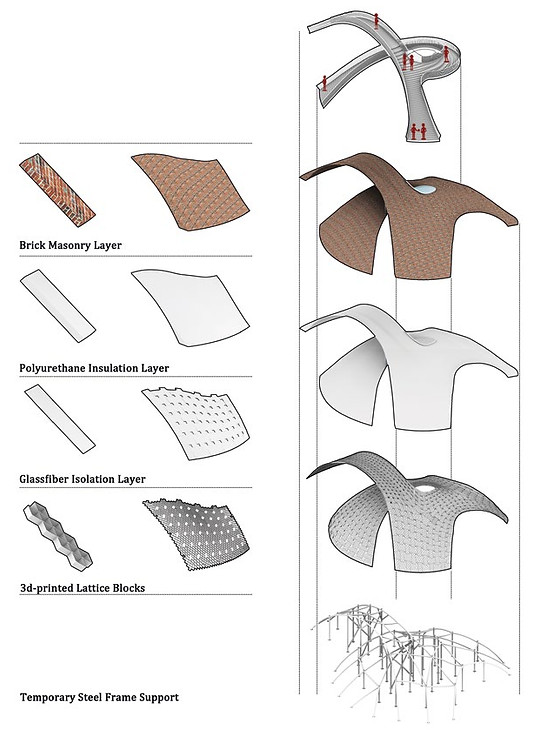
Diagram of the construction details and fabrication sequence of the formwork system.

Design of the reciprocal structure pattern of the 3D-printed formwork system.
The on-site adjustment of the formwork system was finished by simply tuning the shims according to the computational model of the formwork design. After the first adjustment, a full 3D scan of the work was done to check the geometry and the maximum tolerance was controlled in the range of ±2cm which provided enough accuracy for the final masonry work of the brick shell.

Loading test to check the structural response and the safety of the shell.
The red pavilion shows a successful result of the structural-performance-based design framework where both the fabrication technique as well as the structural behavior are taken into consideration. The fast and accurate construction of the red pavilion provides a future for the green construction of large-scale complex shells with an optimized formwork system and the application of eco-friendly materials and fabrication techniques. In the collaboration between the designers and structural engineers, not only a digital modelling strategy but also a wrap-around construction system was developed to fulfill the energy-saving and sustainable building future of the efficient shell structures.
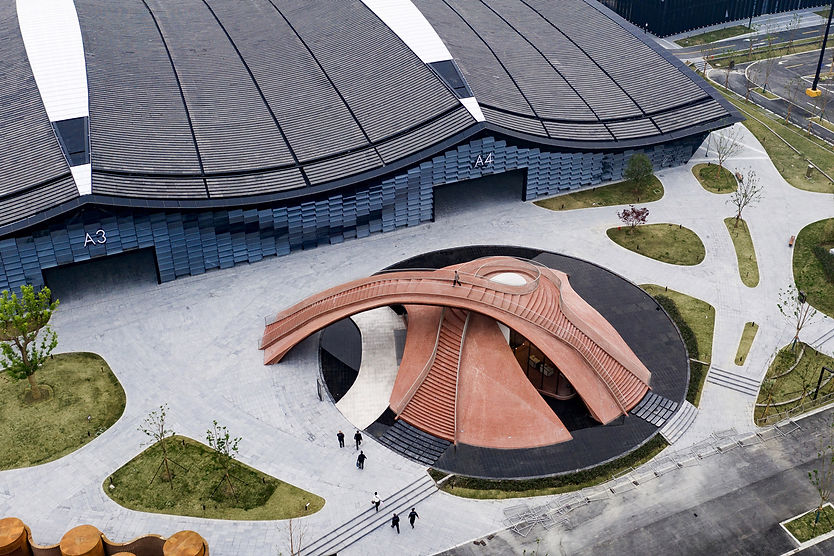